What every oil brand and processor should know about their vaping hardware manufacturer.
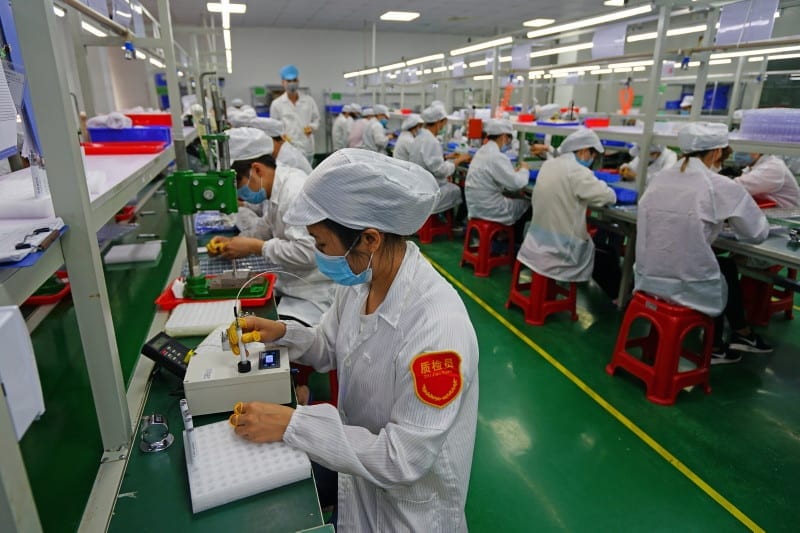
So you can confidently fill and market cartridges and batteries, you require more than empty words from your hardware manufacturer, like:
“We manufacture safe vaping hardware.”
Or,
“Our processes ensure consumer safety.”
Because it’s easy for a cannabis hardware manufacturer to make bold claims.
But instead, what you need, is to see for yourself why ACTIVE legitimately makes and then stands behind these claims. So we’ve thrown open our doors to let you see the inner workings of our factory…
(As an aside, what you’ll read here is not about or in reaction to the Covid-19. Rather, its about the longstanding procedures and systems in place – albeit upped a notch to include even more rigour around personnel safety.)
Let’s kick off with a few comforting acronyms.
ACTIVE manufactures in a sterile, cGMP certified environment. Plus we’re ISO 9001 certified.
What this means is we have quality management and systems in place. These ensure the proper design, monitoring, and ongoing control of our processes and facilities.
For you, however, this means peace of mind. Because you know we are manufacturing to reputable international standards.
But you may rightly ask, “International standards aside, how exactly do you make sure the cartridges you deliver to me are absolutely clean and hygienic?”
It all begins by keeping out pathogens and dust
Manufacturing takes place in ISO certified clean rooms.
Not only because particles of dust and other manufacturing residues might interfere with delicate electronics and cause malfunctions.
But also, to reduce the presence of bacteria.
By the way, a clean room, if you’re not that familiar with one, is a room designed to maintain extremely low levels of particulates – like dust and bacteria.
ISO, in turn, refers to the standards set around quality, safety, and efficiency by the International Organization for Standardization.
(With apologies to the engineers for the oversimplifications.)
With that out the way, here’s a visual of one of ACTIVE’s ISO clean rooms.
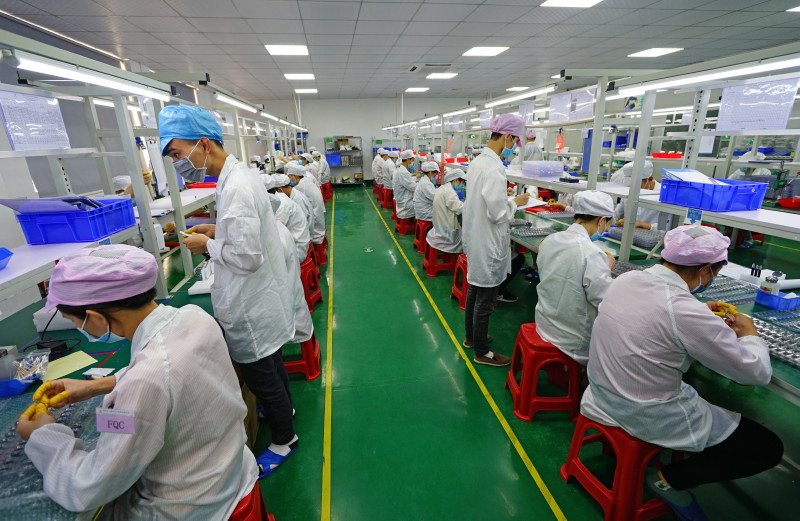
For the more technically minded, you can read about clean rooms here.
To clean the air, we carefully control airflow, air pressure, and air filtering, within and into the clean rooms.
This filters out airborne particulates like microscopic residue that arises from manufacturing and the fresh air entering the workspace.
Then, several times a week, using a dust particle counter, we measure the air purity levels to make sure we’re conforming to the ISO standard.
Why we use strange blue lights
You may have noticed the blue lighting in the clean room above. Here’s a closer look.
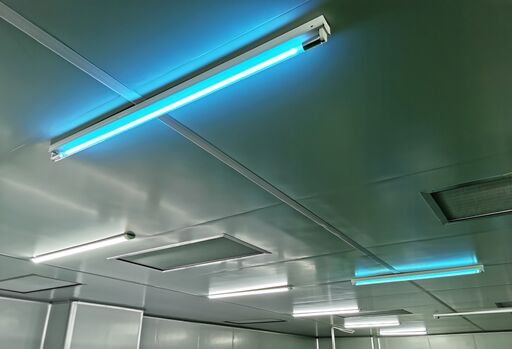
Ultraviolet lamps disinfecting ACTIVE’s clean room
These are ultraviolet sterilization lamps.
Ultraviolet light is one of the most effective ways to destroy viruses, bacteria, and other airborne allergens by breaking down their DNA or RNA.
At the end of each workday, we turn the lamps on once staff leave and then turn them off in time for the next shift.
These lamps are key to how we manufacture safe vaping hardware.
How we take care of germ and dust hitchhikers
You may be thinking, but hold on, what about germs or dust that could hitchhike a ride into the clean room when we bring in raw materials?
Here’s where we go even more high tech.
All materials only enter the workshop after passing through a high-intensity ultraviolet and ozone sterilization shower channel. The shower zaps the bad guys and eliminates the vagrant dust.
You can see one of ACTIVE’s sterilization showers below.
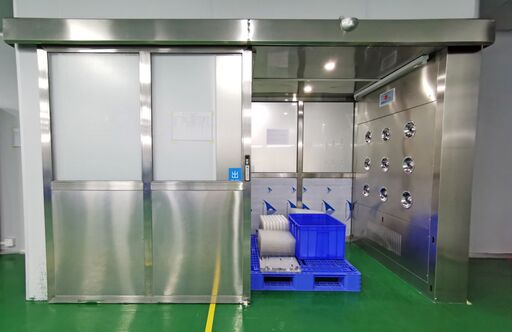
ACTIVE’s high-intensity ultraviolet and ozone sterilization shower channel
Our anti-cross-contamination solution
Things start getting pedantic here.
All materials and products entering the clean rooms are placed 11.8 inches (or for the metric minded folk, that’s 30 cm) from the ground and 3.9 inches (or 10 cm) from the walls to make sure products stay clean.
(Pity the person tasked with the tape measure.)
Once inside the clean room, products are placed on a tray wrapped with plastic. And storage boxes are sealed with a cover to prevent contamination.
Pallets, fixtures, and material boxes that come into direct contact with the products are routinely sterilized using a 75% ethanol disinfectant.
Maintaining sterility to your doorstep
Once the products are manufactured, and before they leave the clean room, they are carefully plastic wrapped and sealed.
This critical step avoids the possibility of contamination during storage and transportation to you.
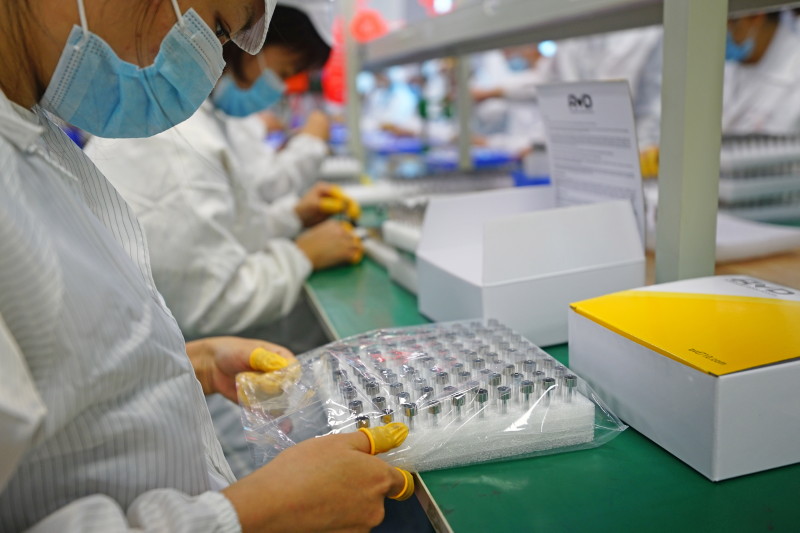
Safety sealing for storage and transport
And now onto the people side of things.
Starting with the uniform
No surprises here.
Anyone who enters the workshop, including the production team, wear clean uniforms.
Not necessarily to show off our logo – although we do love it.
Instead, to prevent body pollutants from contaminating products and minimize the risk of spreading germs amongst our staff.
As an additional measure, team members who have direct contact with atomizer parts wear finger gloves to avoid contamination.
In case you can’t visualize it, we’ve included a staff member modeling the ACTIVE garb. Not flattering, we’ll admit. But highly effective nonetheless.
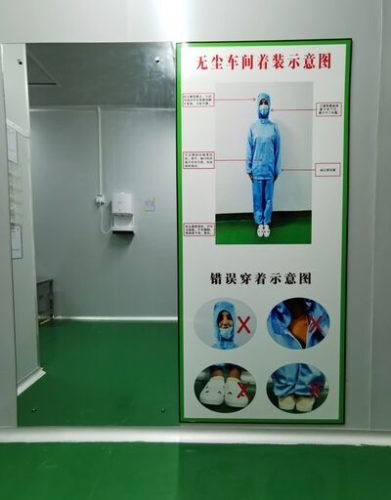
ACTIVE production uniform
The magic of the purification and sterilization wardrobe
The production team stores all their work clothing in a purification and sterilization wardrobe after every shift.
Here’s a picture of our high-tech wardrobe filled with pathogen and dust-busting wizardry.
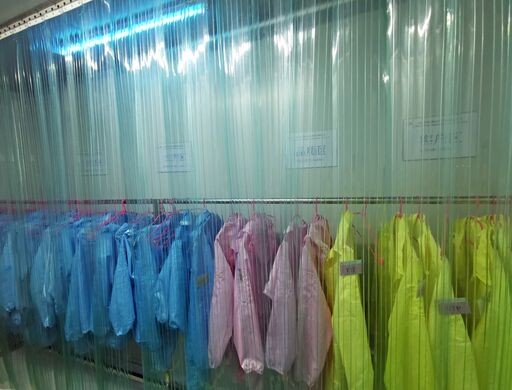
ACTIVE’s purification and sterilization wardrobe
The wardrobe has a 99.99% high-efficiency particulate air (HEPA) filter and ultraviolet germicidal sterilization lamps.
The filter traps and screens out almost every particle. While the ultraviolet lamp sterilizes the clothing, readying it for the next shift.
Hand washing and personnel disinfection
Handwashing, as you can imagine, is taken seriously around here.
Staff entering or leaving the workshop, adhere to strict hand disinfection and washing each time they leave their workstation.
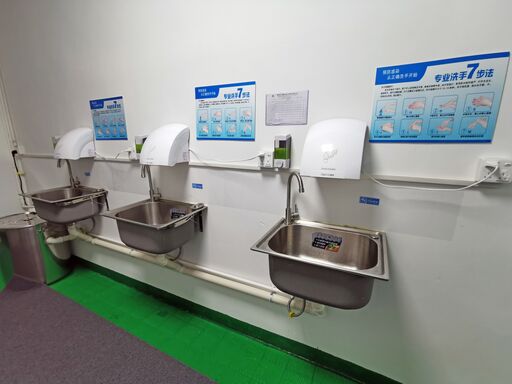
ACTIVE’s handwashing station
Air showers
Beyond handwashing, we also use air showers.
All production staff pass through an air shower before entering the clean-room.
While not nearly as much fun as a flight-simulator, the air shower effectively removes any dust and other residual particles.
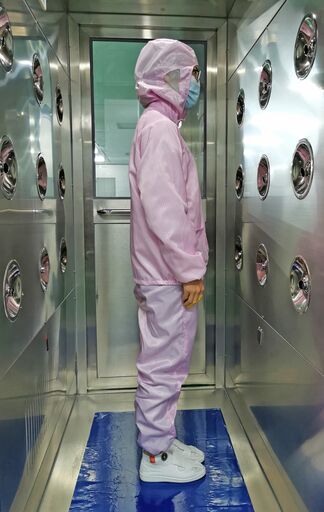
ACTIVE production personnel air shower
Public area disinfection
Every day, the cleaning team scrubs down the production and public areas using some 84 different disinfectants.
Everywhere. Floors, doors, windows, walls, and ceilings.
Nothing is missed as cleaning staff works their way from the handwashing area offices, activity areas, aisles, corridors, the canteen – and elsewhere.
Employee temperature checks
Before starting work each day, and after holiday breaks, staff members undergo an on-the-spot medical examination.
Employees living on the ACTIVE campus, have a temperature check each evening.
While employees living elsewhere and visitors to the ACTIVE factory have their temperatures checked on entry and only allowed in if their temperatures are within a normal range.
So, there you have it. The ins and outs of how we manufacture safe vaping hardware.
Our strict adherence to these protocols is what allows us to vouch for every product that leaves the factory.
And from your perspective, the comfort that you are filling and marketing high quality, reliable – and above all – contaminant-free products.
To find out more about individual ACTIVE products, you can visit ACTIVE’s product page here.
And if you haven’t yet and want to try out sample ACTIVE cartridges and batteries with your extracts, please click here. This link will take you to ACTIVE’s home page where you can request test samples.